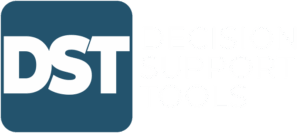
Science-based decision-making just got more accessible and intuitive
Introducing DST v4 – our most advanced upgrade yet.
Elevate your decision-making capabilities and experience.
Discover the future of decision support with DST v4.
Some answers to typical questions.
Yes, we have successfully used the software for all types of assets and equipment from laboratory equipment to large gas turbines even instruments and control systems, from industries as diverse as pharmaceuticals, nutritional products, utilities through to heavy industries, shipping, and oil and gas. For more information visit our Industry Sectors page.
No, we don’t encourage this approach because the data providers often do not know how the data is to be used and more importantly improvement opportunities will be missed. We recommend that only common data items are collected such as hourly rates for technicians and production costs for consistency across decisions, we can provide a list of ‘typical common’ data types on request.
No, the software uses some very advanced financial and reliability mathematics to model the huge variety of decision types that it can handle. In practice, this means that to safely use the software to make decisions for critical assets requires user training. So as part of the software purchase, we will work with you to define your training needs.
The quickest way is to engage a DST-approved consultant who can complete the analysis for you. Depending on the complexity of the decision this could take less than a day to do, providing you have the right people available. You can do this by contacting us now.
Whilst criticality is often used to determine the frequency of individual tasks when applying RCM, it does not accurately account for the often complex trade-offs and interactions between maintenance cost, production losses and failure risks. These are explicitly modelled using DST Asset Strategy Evaluator.
All previously done RCM, FMECA or FTA work done will contribute to DST software inputs depending on their relevance to the problem being solved. For RCM and FMECA, we would expect as a minimum the functional requirements, failure modes and effects to be primary inputs. For more complex systems the effects would be refined by the FTA.
In order to build the economic case with associated timings these inputs would be further refined to include the failure pattern descriptions in terms of probabilities and failure rates which change with time and the associated costs of planned tasks, mitigation and corrective actions. Failure modes will typically be extended to include changes in O&M costs as a result of changing asset condition and where applicable performance/ revenue losses.
This enables you to have a much clearer view on the financial implications of your maintenance strategy backed up with a demonstrable business case. The good news is that all the information that was captured as part of the RCM processes can be directly applied to the DST Asset Strategy Evaluator, so nothing is wasted, consider the application of DST Asset Strategy Evaluator, as the next logical set in your improvement program. If you have yet to start your RCM implementation we recommend that you go straight to DST Asset Strategy Evaluator, it’s a quicker and more effective method of building your maintenance strategy.
DST will effectively build on existing exercises such as RCM/ FMECA and FTA to create a economic business case for your planned interventions. The availability of such data will make the process more efficient.
Risk based inspection, is an excellent approach which complements DST Asset Strategy Evaluator. Whilst RBI is used to determine the frequency of inspections for safety-critical equipment, it does not analyze the often complex trade-offs and interactions between inspection cost, production losses/ downtimes, and failure risks. Neither does it account for process-based inspections which may not have direct safety consequences. These are all explicitly modeled using DST Asset Strategy Evaluator. This enables you to have a much clearer view of the financial implications of your inspection strategy backed up with a demonstrable business case.
Yes, DST Asset Strategy Evaluator, has the unique capability to calculate the optimum replacement timing of your equipment, it can also tell you whether it is worth spending some money to refurbish the asset / equipment and delay the need to replace it.
Yes, DST Asset Strategy Evaluator as shipped has the capability to be used in English, Spanish and French. If you would like it translated to other languages, we can provide the language files and you can translate from English to your own chosen language. This means that the product can display and report in any language you wish.
Discover how the DST EVALUATOR Suite could combine to benefit your organization.
We would be happy to speak with you and learn how we can help you and your business.
Registered Office:
19 Prince Henry House, Kingsclere Business Park,
Kingsclere, Hampshire. RG20 4SW. UK
Cookie | Duration | Description |
---|---|---|
wp-wpml_current_language | session | No description available. |
Introducing DST v4 – our most advanced upgrade yet.
Elevate your decision-making capabilities and experience.
Discover the future of decision support with DST v4.